Halcyon produces parts for the new electric Alpine! Indeed, the automobile manufacturer Renault Sport and the equipment manufacturer Valéo recently established a partnership with the company Halcyon for the design and manufacture of parts intended for vehicle assembly.
The manufacturer chose Halcyon as a partner for the design of small series parts, using incremental forming. This process allows a reduction in the cost of tools by more than 80%.
The Halcyon company has in fact developed know-how in the use of this forming process, particularly for the design and production of complex, high-precision parts.
WHAT IS INCREMENTAL TRAINING?
The principle of incremental forming is as follows: a forming tool equipped with a spherical head will follow predefined contours with continuous movement on the surface of the sheet metal. Gradually, in negative vertical increments, the tool will locally deform the sheet until the final shape.
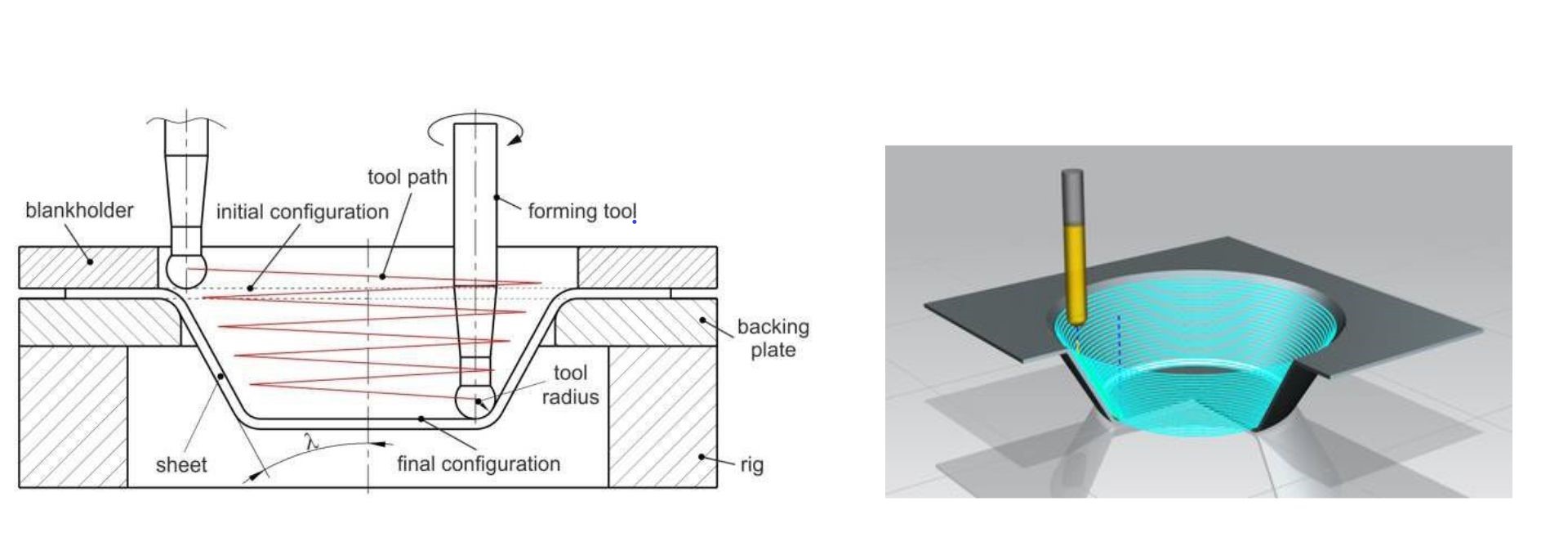
WHAT ARE THE ADVANTAGES ?
First of all, it constitutes a low investment technology. Incremental forming can be easily used on CNC milling machines or robots.
In addition, the process uses simplified tools. Indeed, to form, there is no need for complex and massive tools (punches and dies) as for stamping for example.
Then, incremental forming is a process perfectly suited to small series production or prototyping: the cost of forming tooling is much lower than that of stamping but the cycle time is, however, much higher. This technology is therefore reserved for small productions. For high production, the cost of producing a die is offset by the higher speed of production per part and therefore the lower cost per part; we will then favor the stamping process.
Ultimately, this type of process constitutes a real industrial breakthrough innovation, particularly in the world of the automobile industry.
If you would like more information on our know-how and our abilities to meet your specific needs, the HALCYON team will be happy to answer you!