Space
Structural performance and weight savings: the aluminum honeycomb sandwich structure solution makes its mark in space engineering.
ALUMINUM HONEYCOMB SANDWICHES FOR THE SPACE INDUSTRY
The space industry is looking for lightweight, durable and reliable solutions for the structures of launch vehicles, satellites and orbital systems.
HALCYON’s aluminum honeycomb sandwich structures are the ideal solution, offering numerous advantages.
Indeed, the sandwich principle – combining strong materials with light ones – improves the overall rigidity of a structural part, while making it lighter.
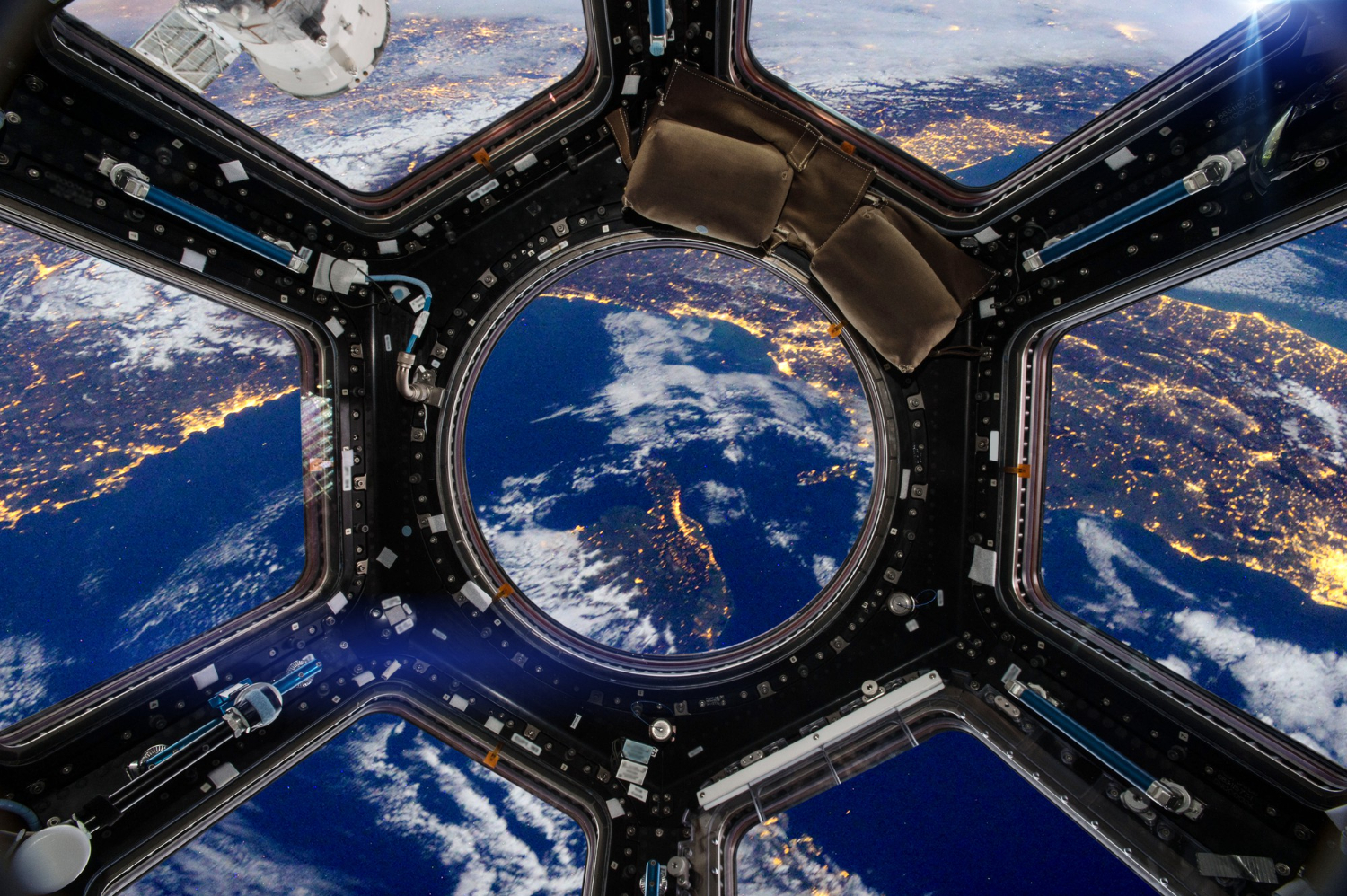
Aluminum honeycomb sandwich materials thus offer many advantages over traditional materials, such as :
Lightweight and high strength
Aluminum honeycomb sandwich panels combine exceptional lightness and mechanical strength, offering an ideal solution for the space industry.
Thanks to their honeycomb structure, loads are distributed efficiently, reducing weight without compromising structural strength. A major asset for the space industry!
In the space industry, every gram counts, with the average cost per kg launched approaching $10,000. Reducing the weight of launchers optimizes fuel consumption and maximizes payload. The aluminum honeycomb sandwich is therefore an essential solution for reducing these costs and improving performance.
This same approach also makes it possible to lighten satellite structures, by focusing on essential on-board functions. A winning choice for the future of space exploration!
Thermomechanical properties
The sandwich material with aluminum skins and aluminum honeycomb offers exceptional thermal stability, making it ideal for demanding environments.
Thanks to its honeycomb structure, it maintains optimum rigidity and resists deformation, even at extreme temperatures. Aluminum, renowned for its thermal conductivity, ensures efficient heat dissipation, minimizing the risk of overheating.
This thermal stability ensures consistent, reliable performance. Structural integrity is preserved, even under the most extreme conditions in space. An essential choice for space applications!
Recyclable
Aluminum honeycomb sandwich panels are distinguished by their high recyclability. Indeed, aluminum can be recycled indefinitely without losing its mechanical properties. This not only reduces demand for raw materials, but also the carbon footprint associated with the production of new materials. The aluminum recycling process also consumes much less energy than the initial production process.
At a time when natural resources need to be preserved, aluminium is an ecological and sustainable choice, not to be underestimated by manufacturers.
Rigidity and stability
Although sandwich structures are lightweight, they offer exceptional mechanical strength.
Aluminum honeycomb sandwich material stands out for its remarkable rigidity and stability. Thanks to its honeycomb structure, it effectively resists compression and bending forces, while maintaining minimum weight.
This structural rigidity enables the material to retain its shape and performance under heavy loads, offering reliable stability in conditions such as take-off.
Its resistance to deformation and mechanical stress makes it ideal for the space industry, where robustness and lightness are crucial.
Vibration absorption
Les vibrations et les chocs sont inévitables et d’une très forte intensité lors du décollage des lanceurs spatiaux. Grâce à leur âme en nid d’abeille, légère et résistante, les structures sandwich absorbent et dissipent efficacement ces forces, assurant ainsi la stabilité et la fiabilité des lanceurs et satellites.
La configuration en nid d’abeille agit comme un amortisseur naturel, dissipant l’énergie vibratoire grâce à sa structure légère et complexe. Cela réduit les résonances, prolongeant la durée de vie des composants sensibles.
Cette capacité à atténuer les vibrations est essentielle dans les applications spatiales, où la sécurité du matériel est primordiale.
Corrosion resistance
Aluminum is highly resistant to corrosion, as a layer of oxide naturally covers it, creating a protective film.
Aluminum honeycomb structures are therefore remarkably durable, even in space environments where temperature variations and exposure to radiation are commonplace.
This material guarantees reliable, long-lasting protection for critical spacecraft components.
PATENTED TECHNOLOGY
Thanks to our expertise in aluminum honeycomb forming and machining, we can produce complex parts to meet our customers’ needs. Whether cylindrical, conical or double-curved, we guarantee exceptional precision and quality, while optimizing part weight and strength. Our know-how enables us to adapt our production methods to the specific requirements of each project.
Today, Halcyon is the only manufacturer capable of forming complex sandwich panels with aluminum skins and an aluminum honeycomb core.
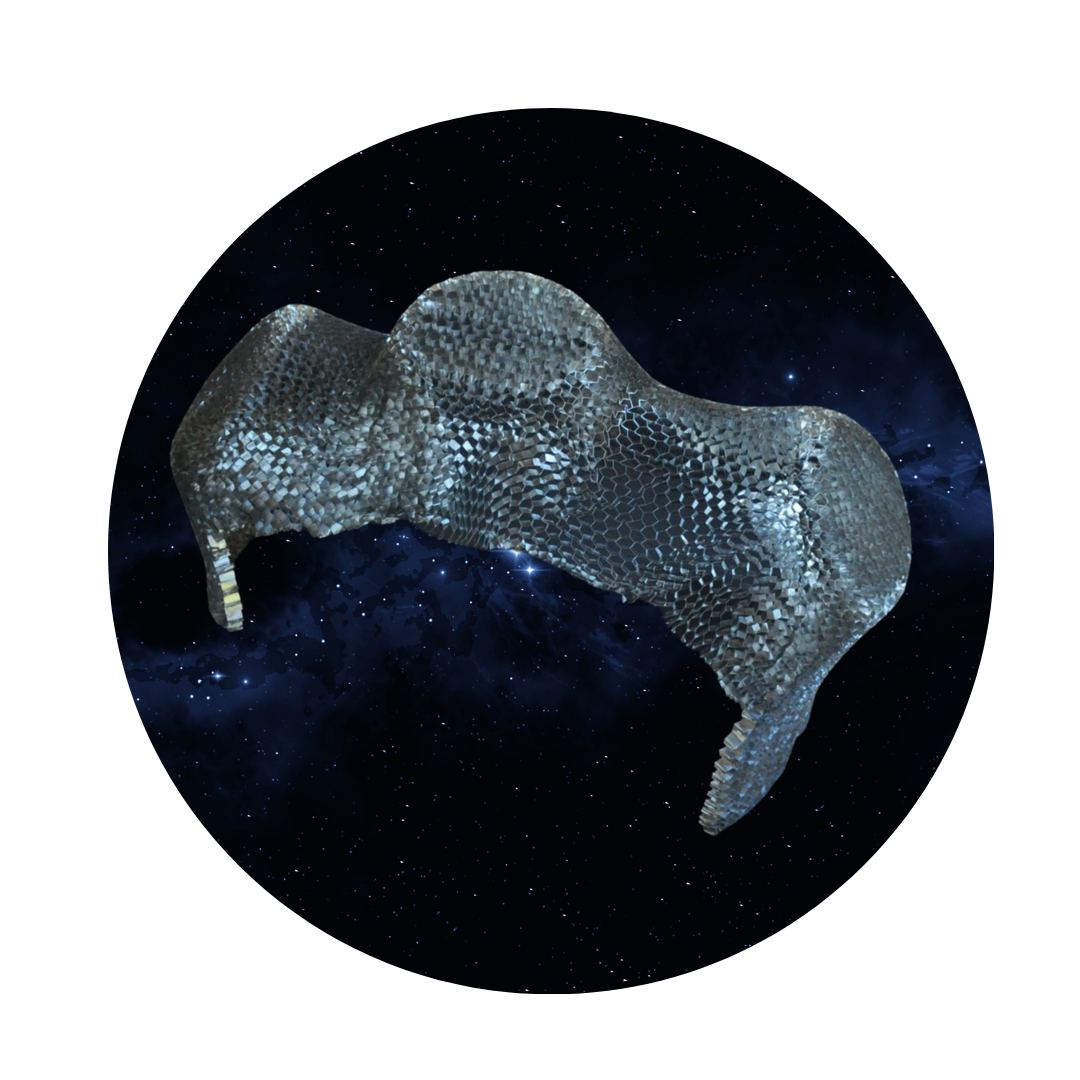
A TURNKEY SOLUTION
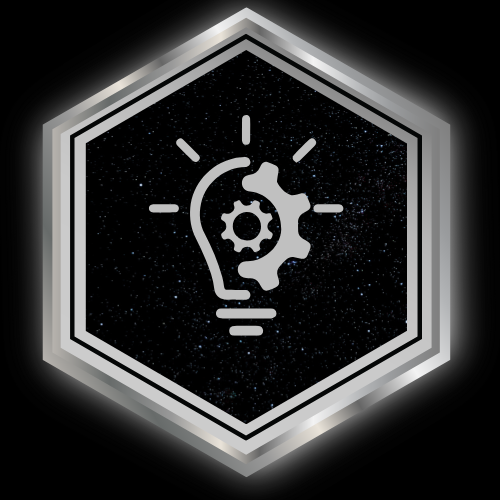
CONCEPTION
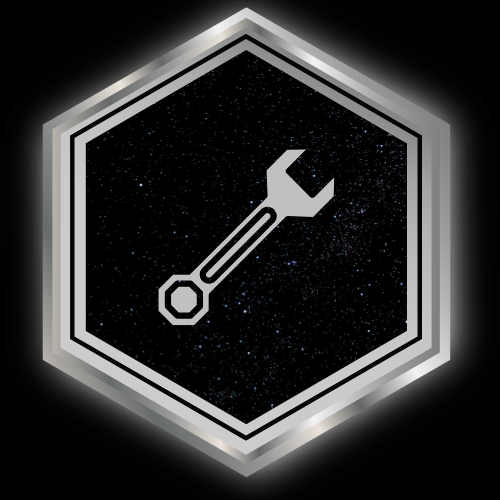
OUTILLAGE
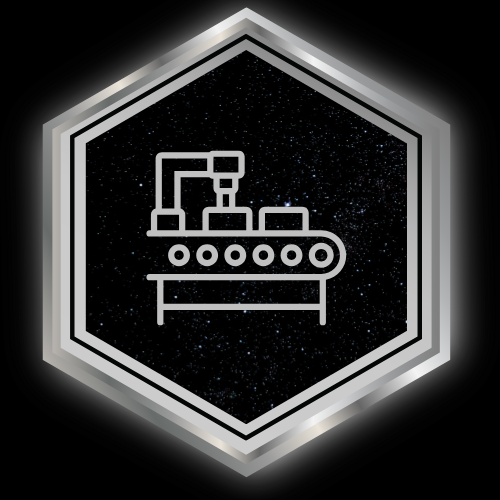
PRODUCTION
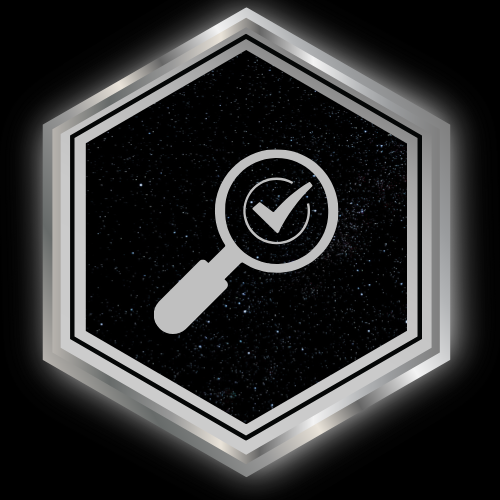
CONTRÔLE
PROCESS ADAPTABLE TO VARIOUS PARTS
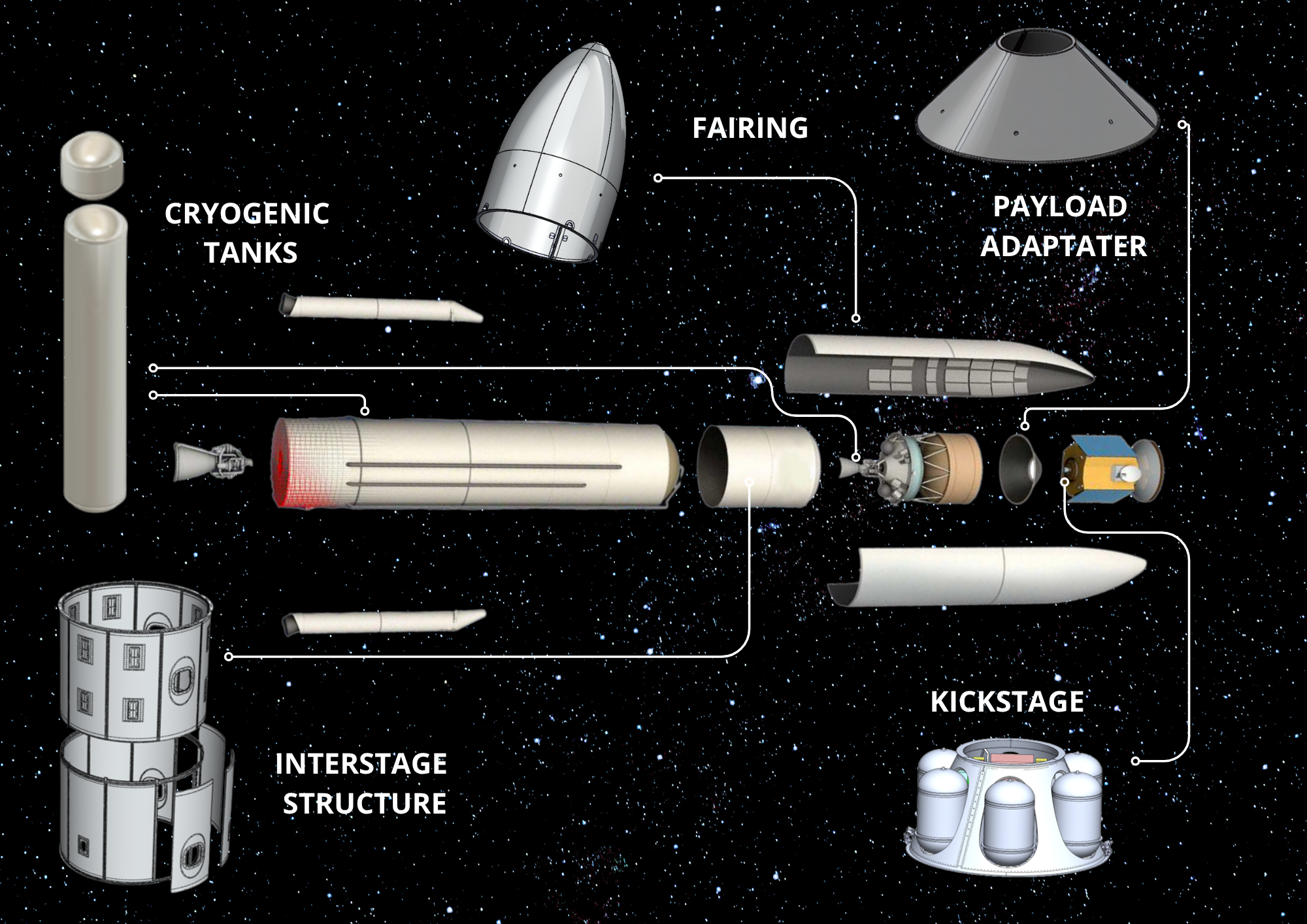
Custom tooling design for the space industry
At Halcyon, every part for the space industry starts with the right tool. We design and produce in-house all the tooling required to manufacture the structures we are commissioned to manufacture – particularly for launchers.
This complete control of the process, from design to manufacture, enables us to guarantee optimum precision, maximum adaptability and controlled lead times. Whether for forming, cutting, fitting or complex assembly devices, our engineering teams develop tailor-made solutions, specifically designed for the unique constraints of the space industry.
Photos: example of tooling developed for the manufacture of structures for space applications.
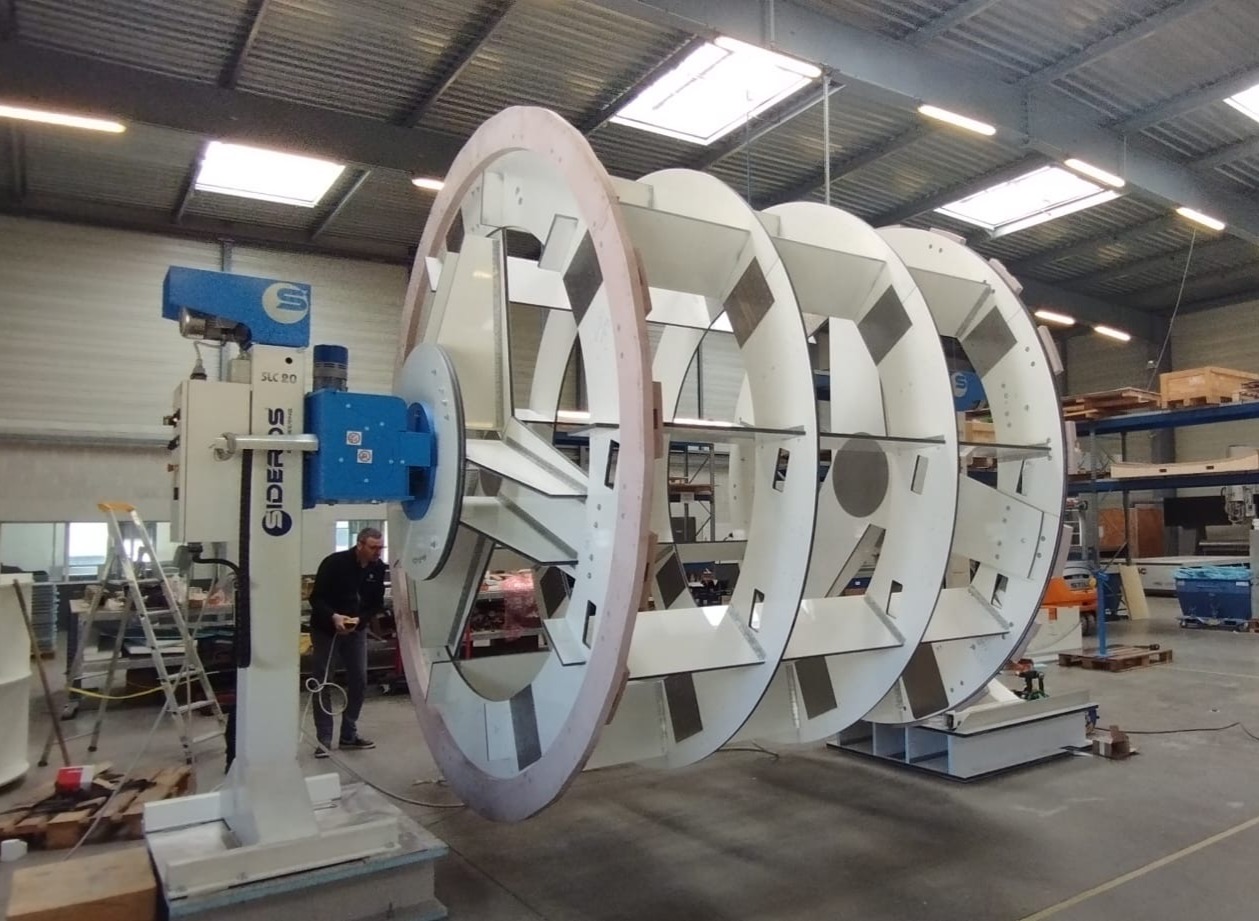
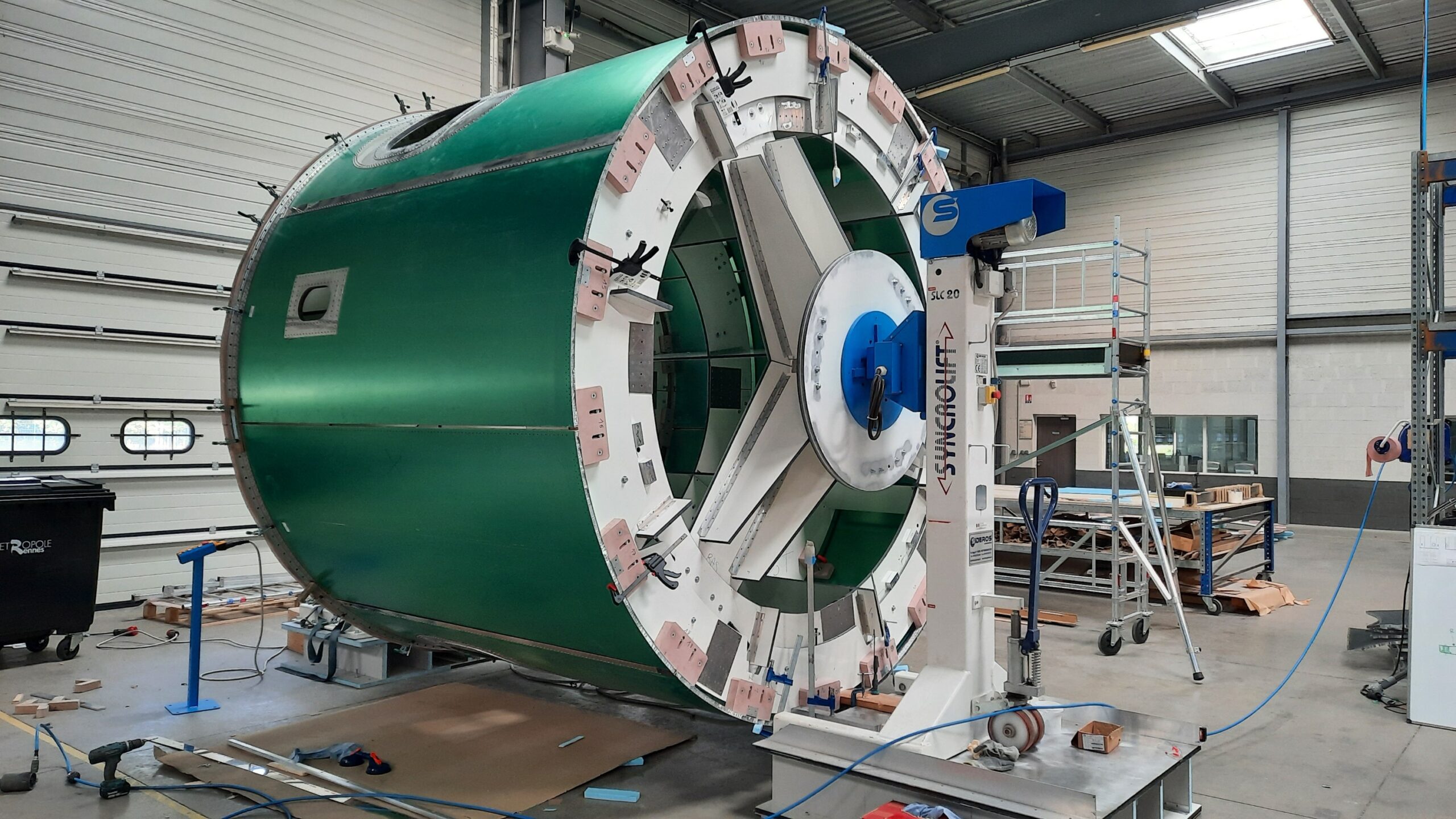
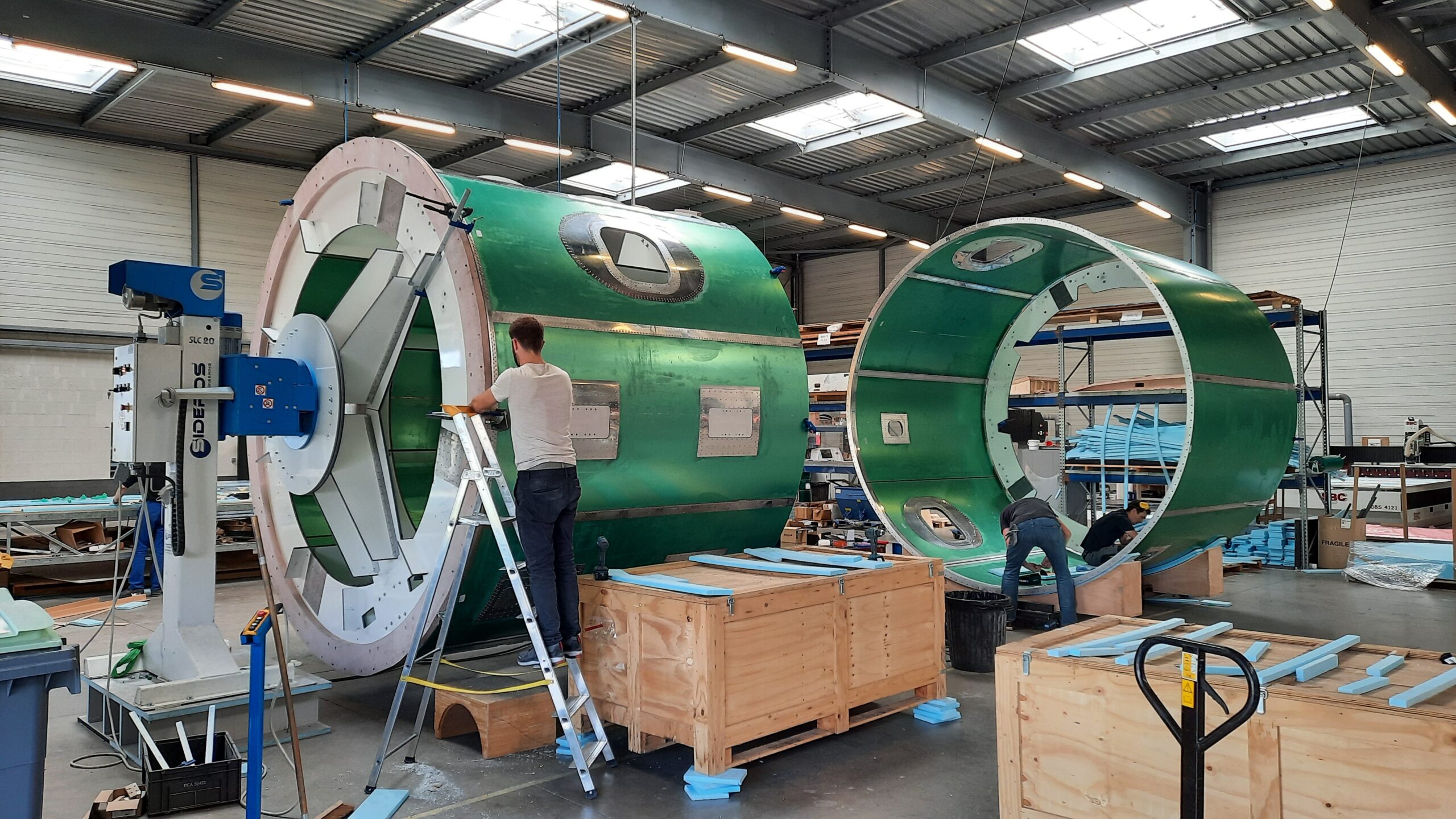